Overview: Computational simulations are like virtual microscopes that allow us to observe, rewind, zoom in, and analyze complex behavior of solids across length scales. Our computational simulations allow us to answer critical questions like: How do the “demographics” of microstructural neighborhoods throughout a given material influence where and when a crack will form? Within a 3D-printed part, where is failure likely to occur? If an infant falls from a certain height at a certain angle, what is the likely skull fracture pattern that results?
In the MMM Lab, we simulate complex and realistic multiscale mechanical behavior in three dimensions by developing and augmenting a variety of numerical tools. Our tools have been used to simulate crack growth in 3D polycrystalline materials, including additively manufactured metals and other aerospace materials, as well as in biological materials, including human bone. Because failure of materials and structures is ubiquitous and can be very costly to society, many funding agencies have supported our research in this area, including the U.S. Department of Defense, U.S. Department of Energy, and the U.S. Department of Justice.
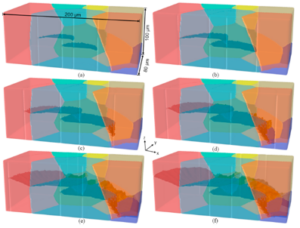
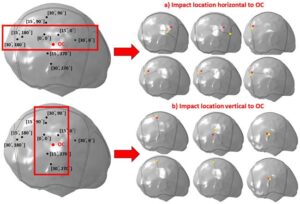
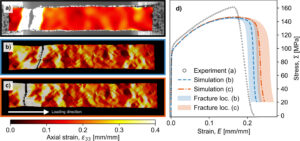
Select publications (MMM Lab members are underscored):
-
Simulation of crushing response in open-cell metal foam using crystal plasticity modeling. C.K. Cocke, H. Mirmohammad, M. Zecevic, B.R. Phung, R.A. Lebensohn, O.T. Kingstedt, A.D. Spear, Implementation and Experimental Validation of Nonlocal Damage in a Large-strain Elasto-viscoplastic FFT-based Framework for Predicting Ductile Fracture in 3D Polycrystalline Materials, International Journal of Plasticity, Vol. 162, pp. 103508, 2023. https://doi.org/10.1016/j.ijplas.2022.103508
- D.F. Zhao, K.E. Matheson, B.R. Phung, S. Petruzza, M.W. Czabaj, A.D. Spear. Investigating the Effect of Grain Structure on Compressive Response of Open-cell Metal Foam using High-fidelity Crystal-plasticity Modeling, Materials Science & Engineering: A, Vol. 812, pp. 140847, 2021. https://doi.org/10.1016/j.msea.2021.140847
- B.R. Phung, J.Y. He, A.D. Spear. A Surface-mesh Gradation Tool for Generating Gradated Tetrahedral Meshes of Microstructures with Defects, Computational Materials Science, Vol. 197, pp. 110622, 2021. https://doi.org/10.1016/j.commatsci.2021.110622
- J.Y. He, J. Yan, S. Margulies, B. Coats, A.D. Spear. An Adaptive-remeshing Framework to Predict Impact-induced Skull Fracture in Infants, Biomechanics and Modeling in Mechanobiology , Vol. 19(5), pp. 1595-1605, 2020. doi.org/10.1007/s10237-020-01293-9
- J. Erickson, A. Rahman, A.D. Spear. A Void Descriptor Function to Uniquely Characterize Pore Networks and Predict Ductile-metal Failure Properties, International Journal of Fracture, Vol. 225, pp. 47-67, 2020. doi.org/10.1007/s10704-020-00463-1
- C. Herriott, X. Li, N. Kouraytem, V. Tari, W. Tan, B. Anglin, A.D. Rollett, A.D. Spear. A Multi-scale, Multi-physics Modeling Framework to Predict Spatial Variation of Properties in Additive-Manufactured Metals, Modelling and Simulation in Materials Science and Engineering, Vol. 27, pp. 025009, 2019. doi:10.1088/1361-651X/aaf753
- B.R. Phung, A.D. Spear. A Voxel-based Remeshing Framework for the Simulation of Arbitrary Three-dimensional Crack Growth in Heterogeneous Materials, Engineering Fracture Mechanics, Vol. 209, pp. 404-422, 2019. doi.org/10.1016/j.engfracmech.-2019.01.008